As a property owner or manager, maintaining the integrity of your building’s envelope is essential for keeping your occupants safe and comfortable. One of the key components of an effective building envelope inspection is using sealants. Why is that? Sealants help prevent air and moisture infiltration, leading to costly damage and health hazards. But with so many sealant options on the market, how do you choose the right one? Learn everything about sealants to ensure you make an informed selection for your building envelope inspection.
Types of Sealants Available in the Market
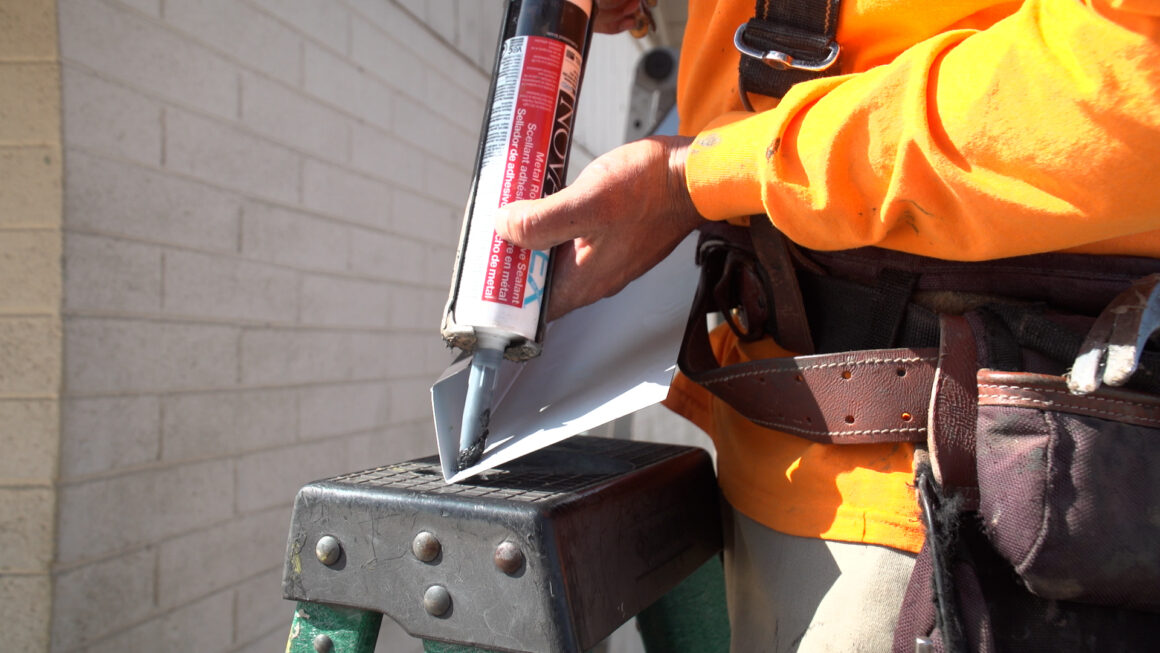
Several different types of sealants are available on the market, each with unique properties and applications. Some of the most common types of sealants include:
- Silicone sealants: These are highly flexible and durable, ideal for use in high-temperature and high-moisture environments.
- Polyurethane sealants: These are also flexible and durable but typically used in lower-temperature environments.
- Acrylic sealants: These are water-based sealants that are easy to apply and clean up but less durable than silicone or polyurethane sealants.
- Butyl sealants: These are synthetic rubber sealants that are highly resistant to water and weathering but not as flexible as silicone or polyurethane sealants.
Choosing the right type of sealant for your specific application is important, as using the wrong type can lead to premature failure and other issues.
Factors to Consider When Choosing a Sealant for Building Envelope Inspection
When selecting a sealant for your building envelope inspection, there are several key factors to consider, including:
- Compatibility: The sealant should be compatible with the materials it will be applied to, such as wood, metal, or concrete.
- Weather resistance: The sealant should withstand the local climate and weather conditions, including temperature fluctuations, rain, snow, and UV exposure.
- Movement capability: The sealant should be able to accommodate the movement of the building materials without cracking or pulling away.
- Cure time: The sealant should cure within a reasonable time to ensure proper bonding and performance.
- Cost: The sealant should be cost-effective and fit within your budget.
By carefully considering these factors, you can choose a sealant that will provide optimal performance and longevity for your building envelope.
Environmental Considerations of Sealants
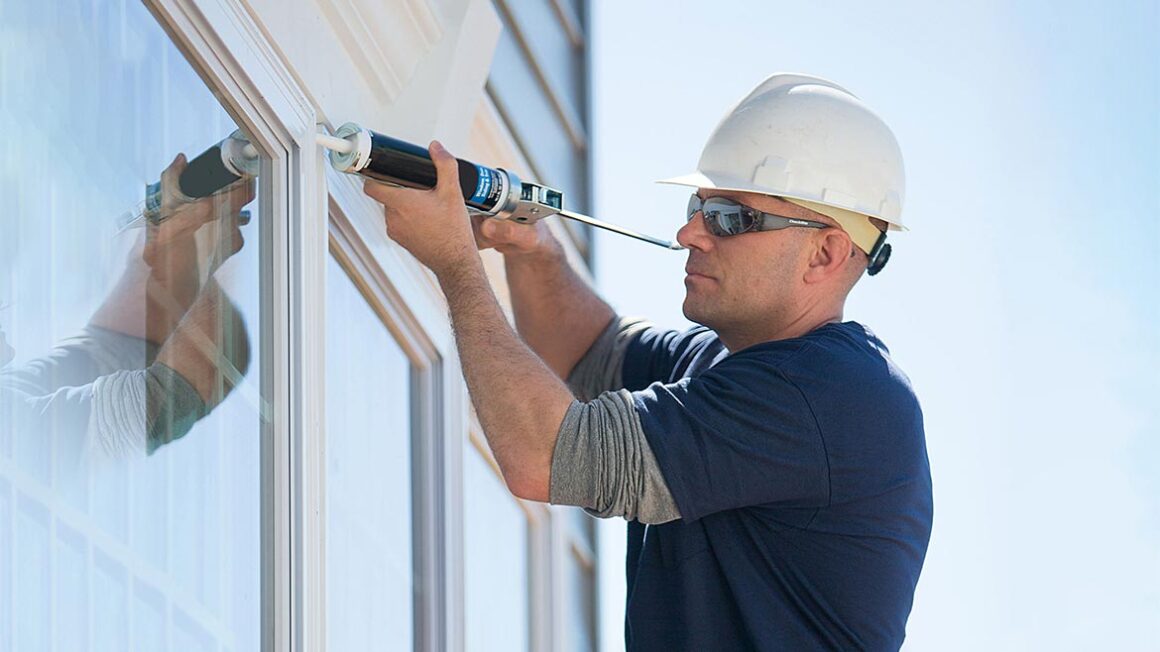
In addition to the functional properties of sealants, it’s also important to consider their environmental impact. Some sealants contain volatile organic compounds (VOCs). They can release VOCs and other pollutants into the air, contributing to indoor air pollution and health hazards such as headaches, respiratory issues, and allergies. Thankfully, low-VOC or zero-VOC sealants are available, which can help to improve indoor air quality and reduce the environmental impact of your building envelope.
However, it’s also important to ensure that sealants are properly installed and maintained to prevent leaks and other issues that can compromise air quality. Furthermore, it’s imperative to dispose of sealant waste properly, as some types of sealants can be hazardous to the environment. Check with your local waste management authority for guidance on how to dispose of sealant waste safely and responsibly.
Understanding Sealant Life Cycle
Like all building materials, sealants have a finite lifespan and will eventually need to be replaced. Understanding the life cycle of sealants can help you to plan for maintenance and replacement, which can help to prevent costly damage and improve the performance of your building envelope. The life cycle of a sealant typically consists of four stages: application, service life, deterioration, and failure.
- Stage 1 – Application: During the application stage, the sealant is applied to the building envelope according to the manufacturer’s instructions.
- Stage 2 – Service Life: The service life stage is when the sealant performs as intended, providing a barrier against air and moisture infiltration.
- Stage 3 – Deterioration: The deterioration stage is when the sealant begins to degrade due to exposure to environmental factors such as UV light, weathering, and temperature fluctuations.
- Stage 4 – Failure: The failure stage is when the sealant can no longer provide an effective barrier and must be replaced.
By understanding the life cycle of sealants, you can plan for maintenance and replacement to ensure the ongoing performance of your building envelope.
How to Apply & Maintain Sealants
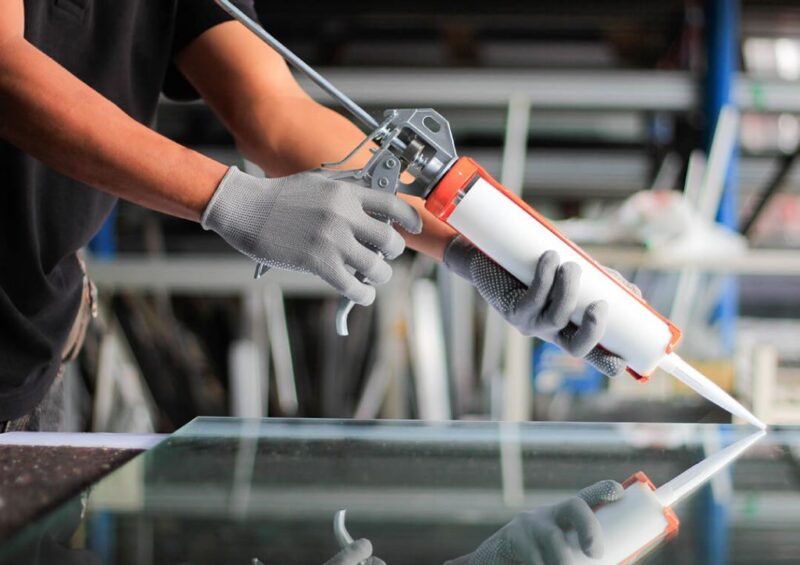
Proper application and maintenance of sealants are critical for ensuring their effectiveness and longevity. When applying sealants, it’s important to follow the manufacturer’s instructions carefully, including proper surface preparation, application techniques, and curing times. Sealants should be applied in a continuous bead and tooled to ensure proper bonding and adhesion. Regular maintenance is also important for ensuring the ongoing performance of your sealants. Inspect your sealants regularly for signs of damage, wear, or other issues, and repair or replace them as needed. Clean your sealants regularly to prevent the buildup of dirt, debris, and other contaminants that can compromise their performance.
Sealant Testing & Inspection
Testing and inspection are important components of building envelope maintenance, and sealants are no exception. Regular testing and inspection can help to identify issues with your sealants before they become major problems, preventing costly damage and improving the performance of your building envelope.
Common tests and inspections for sealants include:
- Visual inspections
- Water testing
- Air leakage testing
- Adhesion testing
Work with a qualified building envelope professional to develop a testing and inspection program that meets the specific needs of your property.
Common Sealant Issues & How to Fix Them
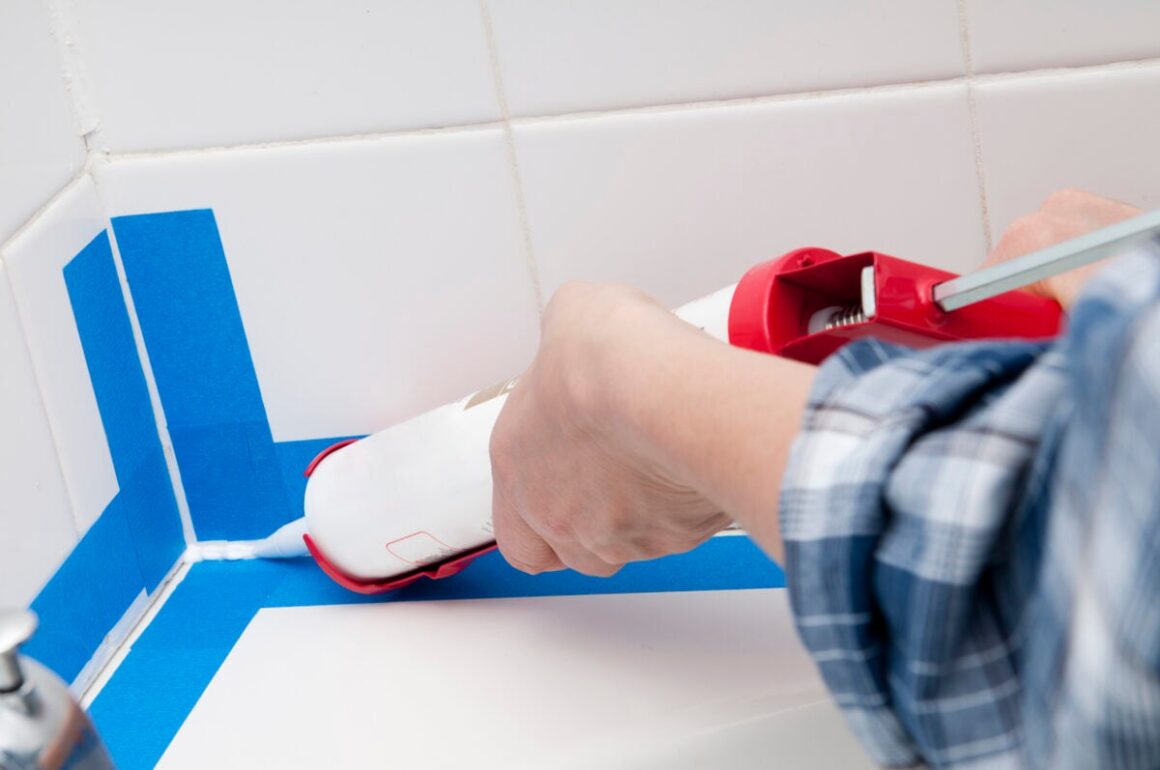
Sealants can still experience issues that compromise performance despite proper application and maintenance.
Common problems with sealants include:
- Cracking
- Pulling away from the substrate
- Discoloration
These issues can often be repaired by removing the damaged sealant and replacing it with a new bead. It’s important to address sealant issues promptly to prevent further damage and ensure the ongoing performance of your building envelope.
Choosing the right sealant for your building envelope inspection is a critical decision that can significantly impact the performance and longevity of your property. By considering these factors and making an informed decision about what sealant to use, you can help ensure the safety, comfort, and longevity of your property for years to come.